In August of 2015, National Public Radio reported on Toyota’s charitable foundation’s partnership with a not-for-profit healthcare system. The decision raised many eyebrows, as some questioned whether an automobile manufacturer knew about healthcare operations. What appeared to be an odd couple on the surface, turned out to be a powerful relationship that redefined partnerships across industries.
The partnership wasn’t aimed at fundraising but rather for process improvement. In one simple example, supply areas were cleaned up and reorganized in the healthcare organization so that nurses were able to find what they needed when they needed it. The time to prepare an operating room was significantly reduced and the nurses reported being less stressed.
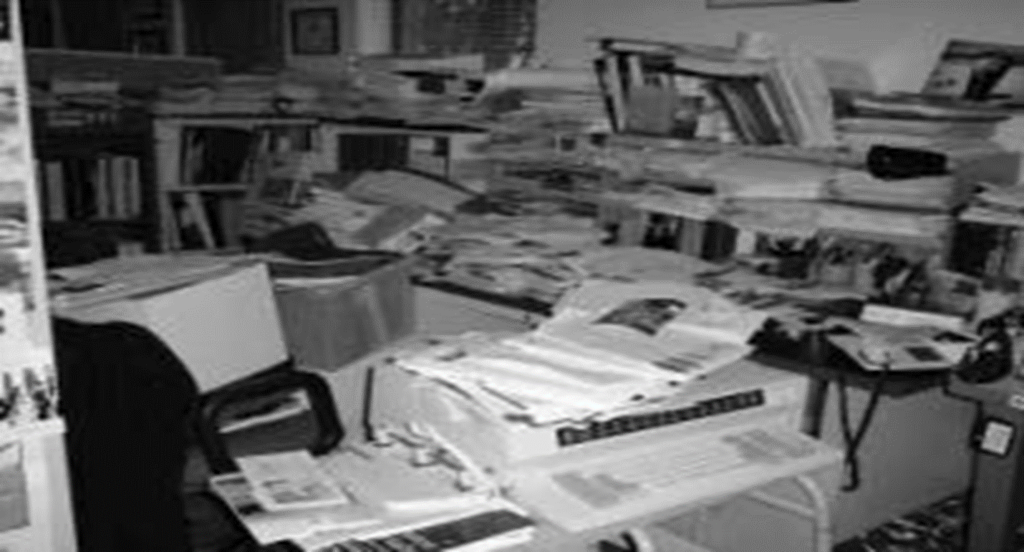
An actual photo of a records room. Can you find the million dollar contract? Neither could they.
The engine behind the process improvement was a hallmark of Toyota’s culture. Called “Lean Methodology,” the philosophy is aimed at eliminating wasteful steps in business processes–essentially doing more with less. This wasn’t an entirely new concept in healthcare, as private hospitals had used Toyota’s lean methodology more than a decade prior. It was, however, new to the not-for-profit healthcare industry–a segment of the industry that drastically changed when the Affordable Care Act passed.
While a well-refined manufacturing system can help build cars faster, proper adoption of lean methodology in healthcare can save lives. It can be the difference between a patient going blind because of awaiting surgery, versus restoring their vision due to efficient processes.
But it’s not just healthcare. There is a long list of industries where lean or a similar philosophy would translate to a variety of process improvements. The main question to ask is “What am I doing now?” Identify the “should be” and the “in reality” workflows for the process in question. Most of the time, there will be exceptions to the rule which need to be identified:
- Why do the exception processes exist?
- What tools are in use?
- Why are they being used?
- Who else is impacted by the process?
- How do you know when the process is complete?
- When do you know the process has been completed?
- What happens when the process can’t be completed?
- What other processes does this process feed?
- What other industries have a similar process? For instance, invoice processing, personnel onboarding, payment processing, procurement and reporting are found in all industries……What are they doing?
In the case of the healthcare system–labeling shelves, using color-coded folders, placing most commonly used items in front, removing obsolete supplies and providing better lighting–all contributed to providing better healthcare.
As a trusted partner in the world of digital transformation for more than 40 years, Western Integrated Systems has observed a variety of consistencies within our own industry.
- Distributed scanning environments in which more than one user will use a device, whether it’s a scanner or multi-function device, will benefit from a coversheet, whether hardcopy or electronic, which identifies who scanned the document so that if there is a problem with the images, the recipient can contact the scan operator for clarification or a rescan.
- Scanning at the point of receipt works best when the person doing the scanning has been trained on the importance of document order.
- Continuous process improvement requires dates to be captured and maintained during the lifecycle of a workflow so that measurements can be taken. Just capturing the start date and the end date doesn’t provide enough information on bottlenecks.
- Data quality and integrity are critical to automating any process.
- Exception handling has to be defined and planned for so the work doesn’t stop.
If you are a document-intensive operation, many of these may be familiar. Some may sound simple, but something as small as an untrained employee operating a scanner can bottleneck entire workflows. It’s an intricacy of your business that can be easy to miss, but something that lean methodology doesn’t take lightly.
If these are issues that are slowing your business down, contact the experts at Western Integrated Systems for a consultation.
0 Comments